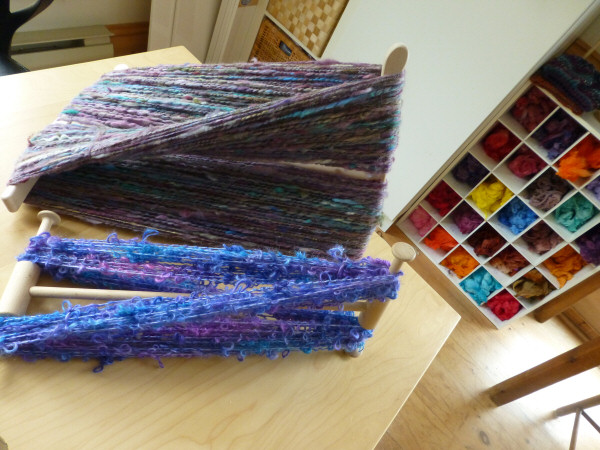
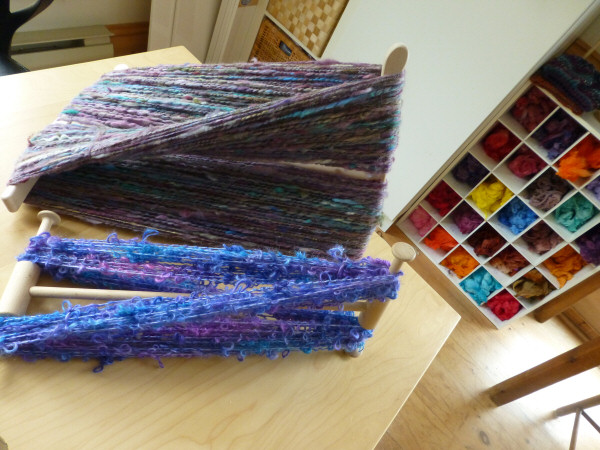
I love that spinning accessories are relatively inexpensive – and are often times handcrafted. You can easily purchase a drop spindle and get started spinning without the investment in a spinning wheel (I know this will mortify spinning purists, but I hate the drop spindle. I broke the cardinal rule of spinning & bought a spinning wheel before ever mastering the spindle).
A niddy noddy is one of those inexpensive but must-have tools. It has a very amusing name. I picture someone a few hundred years ago, designed a skein wrapping tool and when asked what it was called, “niddy noddy” was what they came up with while put on the spot. Perhaps this nonsensical name has a clear meaning and if so, do tell! 😉
If you are still wondering what a niddy noddy is, it is a wrapping tool used to make skeins of yarn after spinning. They are traditionally made of wood, but I have seen homemade varieties made out of PVC pipe, and even metal/wood hybrids. There is one central bar where you hold it, and crossbars at each end that are offset from each other by 90 degrees. Here in North America, niddy noddies are most known to come in 1 yard and 2 yard lengths. I prefer to use the 2 yard length on my Lendrum niddy noddy. Before removing the skein I count the wraps & multiply by 2 to give me the length in yards.
Making more and more funky art yarn on my Spinolution wheel these days, I was finding the Lendrum niddy noddy to be too small to fit some of my skeins. I would make them fit, but it was not easy. I was excited to find that Ashford had a jumbo Niddy Noddy. I purchased mine from Gemini Fibres for $39.
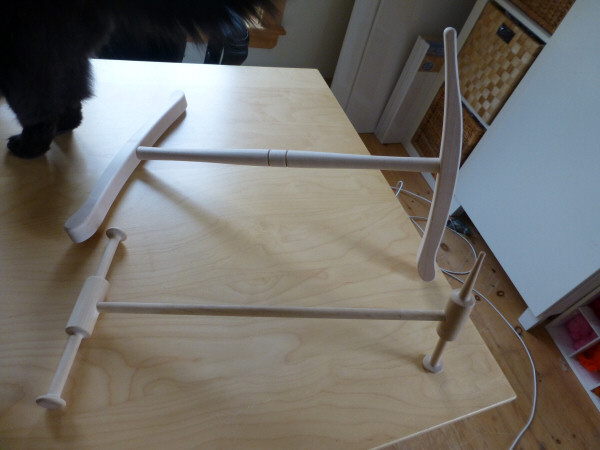
I’ve put in a lot of hours with my Lendrum and can pretty much wrap without thinking (it takes a bit to get the right rhythm the first few times). Due to the larger size of the niddy noddy jumbo it took a bit of getting used to all over again. The pro is that I don’t have to worry about running out of space when skeining my bulky art yarns. It holds over 1 kg (2.2lbs) of yarn. The cons are that it is heavier and more cumbersome to use compared to my standard Lendrum. I also like that my Lendrum has notches on the cross bars so that if I need to squeeze the wraps together more tightly they are not overlapping the wraps on the other side which can get confusing when you pull off the yarn or tie it off.
Another quirk is that, coming from New Zealand I have to remember that this niddy noddy measures in metres and not yards. So when counting wraps if I forget and calculate yardage rather than converting the meter length to yards (1 metre = approx. 1.09 yards) I will end up with more yarn per skein. This is not a bad problem to have of course, but I like to try to be exact so that I can keep track of my materials & how long it takes me to spin it.
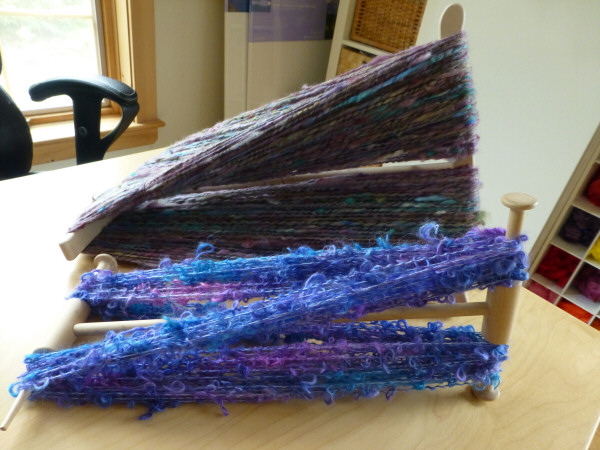
Despite its nuances I am really happy to add this tool to my studio and suspect I will use it very often in the coming months.